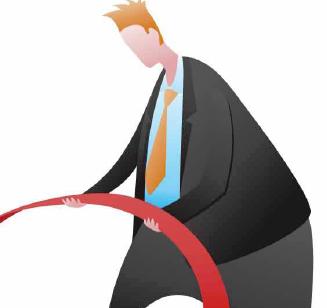
Businesses can protect their reputation and boost their chances of survival by tightening up the supply chain, as John Kinge, head of Risk at Exor Management Services (EMS), explains.
A solid reputation is paramount in ensuring a company’s longevity. Even when business is slow due to external financial pressures, a good reputation will stand an organisation in good stead for the economic upturn. A good reputation can result in healthy profits and a consistent flow of business—which is why there is a multi-billion pound industry devoted to managing reputation and handling any crisis that threatens to damage it. Once the damage is done, it can be very difficult to recover.
History has produced examples of hugely successful companies who have failed because consumers and shareholders have lost faith. Pan Am airline, for example, suffered a string of terrorist hijackings in the 1970s and 1980s including the infamous Lockerbie bombing. This resulted in passengers losing trust in Pan Am’s safety record and the airline as a whole.
It is very common for businesses to outsource many different services if they do not have the resources or expertise internally. It can also be a more cost effective option. The list of suppliers can be endless, including cleaners, IT engineers, maintenance, contractors, manufacturers, accountants, HR professionals and so on. When procuring external services, many buyers are concerned with how cost effective they are and whether or not they will help a business achieve its bottom line. But what about a supplier’s corporate social responsibility (CSR) and equal opportunities credentials, or health and safety record? The reputation of a supplier can have a knock-on impact on a buyer’s reputation and if things go wrong, it can threaten to derail the entire operation.
Recently, several high street retailers came under fire when it was exposed that a factory in Leicester, UK, where some of their clothes were manufactured, was employing people under appalling conditions. Many of the textile workers were Asian students who were, in many cases, paid below the £5.93 minimum wage. One report described the workshop as dirty, cramped and poorly lit, with staff being threatened with the sack if they didn’t work quickly enough. There was also a claim that no effort was made to check employees’ legal status and right to work in the UK.
On paper, many of the retailers were supporters of ethical business and are members of the Ethical Trading Initiative. Their efforts in using UK-based factories where possible rather than outsourcing to factories abroad was undermined by this scandal and has called the brand’s CSR credentials into question. The retailers placed the blame with the supplier who engaged with the factory but arguably, it is the big name buyer that will suffer the most in terms of reputation damage.
This rather extreme example demonstrates how buyers can be twice, or even three times removed from the supply chain—and some suppliers may even subcontract further. This opens up buyers to increased risk and it is therefore important to keep control on activity where possible.
So why do businesses outsource in the first place?
Companies outsource for a number of reasons, all with the aim of improving their overall business performance. Many outsource to reduce costs where they can and find the same quality of service for a cheaper cost. Another key reason is to improve business focus as outsourcing a particular service increases a company’s flexibility and enables it to focus on its core competencies. This relieves pressure on internal resource and increases the volume of work that can be completed.
Public sector organisations such as local authorities are obligated to fulfill government policy that stipulates 25 per cent of contracts must be outsourced to SMEs within the private sector in order to stimulate and offer support to smaller businesses. Working with a number of suppliers can strengthen a company’s operations, providing cost effective solutions and a widened service offering. But any extensive supply chain needs to be managed carefully, so that a company can legally protect itself from a breach in conduct by a supplier.
Many companies are now waking up to the potential for major cost reduction and service improvement offered by implementing best practices in their supply chain. Supply chain management is now considered a critical business process for companies in order to get the best results. Part of managing the supply chain should involve checking a number of compliance issues that, if breached, could threaten a company’s reputation and position in the marketplace. These include health and safety procedures, corporate social responsibility (CSR), equal opportunities policy and finance.
A third party accreditation scheme can be an efficient way in which to manage complex compliance issues. The schemes assess, review and audit suppliers, procedures and documentation. Suppliers can then be included on a database which demonstrates they have met the highest standards in the marketplace. It allows the company at the top of supply chain to have the confidence it needs to outsource vital services, removing the hassle of verification and providing peace of mind that it is adhering to regulations. Managing a complex network of suppliers can place additional strain on internal resource and may not be thorough enough; using accreditation schemes allows a business to have a strategic view of its supply chain, thereby reducing cost and risk.
In today’s uncertain economic climate, businesses cannot afford to be complacent about the activity of the suppliers they use. Legislation and compliance criteria are increasingly intricate and extensive, so organisations need to be extra vigilant. It is clear to see the negative impact on a business when suppliers fall foul of regulations. The reputation and profitability of an organisation is more and more reliant on the practice of suppliers, so it makes good business sense to ensure suppliers reflect similarly high standards in terms of quality.
John Kinge is head of Risk at Exor Management Service (EMS). EMS helps buyers reduce risk and cost by procuring services efficiently and helps suppliers win business in a competitive global market. It works with 20,000 contractors and suppliers and around 250 buyers including many local authorities. www.exorms.co.uk