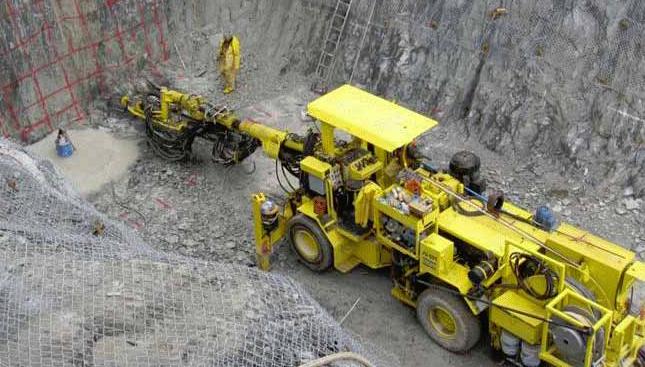
A major investment in IAMGOLD’s Westwood Project in northern Quebec will also benefit from facilities left behind by neighboring mines in the area.
IAMGOLD is a mid-tier gold mining company producing around one million ounces annually from eight mines on three continents. With a rich pipeline of development and exploration projects, IAMGOLD employs roughly 5,000 workers in West Africa, parts of South America, and the Canadian provinces of Ontario and Quebec, where it also operates a niobium mine.
Established in 1991 as International African Mining Gold Corporation, IAMGOLD is actually headquartered in Toronto, Canada. The company returned record results in 2010 for net earnings, adjusted net earnings and operating cash flow. Gold production of 967,000 ounces increased by 3 percent over 2009, but to secure the company’s future, as resources are mined, new mines must be developed to replace them.
The Westwood Project, acquired by IAMGOLD in late 2006 as part of the acquisition of Cambior Inc, is located on the Doyon property in the Abitibi region of Northern Quebec, 2.5 kilometers east of the Doyon Gold Mine in the Bousquet Township, approximately 80 kilometers west of Val d’Or.
Gold production has been in decline at the Doyon division after the closure of the Doyon mine itself in December 2009 and reduced production at the Mouska mine which is nearing the end of its life.
There is still gold in the area, however, and the Westwood project is on track to commence commercial production in early 2013.The Westwood project is part of the Doyon-Bousquet-LaRonde (DBL) mining camp which is recognized as Quebec’s largest gold–copper–zinc–silver producing district, hosting some 25.5 million ounces of gold.Mineralization has been identified at Westwood from a 60 meter depth to as deep as 2,600 meters, within three sub parallel zones that extend along a strike length in excess of 1.8 kilometers.
In April 2009, an 837 meter raise bore was completed as the shaft pilot hole, becoming the longest 2.4 meter diameter single-pass raise bore in the world. Of the $86 million expenditures in 2009, $38 million was related to site preparation, $15 million to shaft sinking, $14 million to the ventilation raise boring and other development, $10 million to general mine services and $9 million to the 84,000 meters of exploration and resource development diamond drilling completed at Westwood during the year.
Almost $95 million was invested in 2010 oninfrastructure preparation and construction, including a 2,000-tonne silo, the permanent ventilation system and the installation of the two hoists that are required for an exploration shaft deeper than 1,200 meters. Shaft sinking began in July 2009 and reached 1,063 meters by the end of the year. The target for the end of 2011 is 1,560 meters, with 2000 meters being achieved in 2012.
Further development slated for this year is to complete the construction of the surface waste silo to allow ore development to begin by the end of 2011, and carrying out an 82,000-meter infill and extensions drilling program for resource development. Already this year, project expenditure in the first quarter came to $27.5 million, including the completion of a number of hoist elements, the fire detection system with the new pump house, final breakthrough of the six-meter diameter ventilation shaft completed and the installation of ground support infrastructure. Shaft sinking reached 1,157 meters, with the excavation of a spill pocket and the safety bulkhead, and underground development work including 2,106 meters of lateral and vertical excavation was achieved.
Once the mine is in production it is expected to average around 186,000 ounces of gold per year at cash costs of around $358 per ounce. It has a current indicated resource of 269,000 ounces with an inferred resource of 3,647,000 ounces, giving the mine a life expectancy of around 16 years.
Mining of the Westwood project was planned using the long hole retreat method. All the stopes will require backfill in order to maintain stability and low dilution. Paste backfill combined with the use of rock-fill was the option retained, which was the method also used at the adjacent Doyon mine.
Having near neighbors in the IAMGOLD family will be a great benefit to all stakeholders, as the plan is to use the main pit from the Doyon mine as a tailings pond, allowing the current tailings pond to be closed and after the pit is capped, making it usable land again. The Doyon Mine was started in the 1970s before acid rock drainage problems were properly understood, and although a costly water collection and treatment system was subsequently installed, waste material from Westwood will further reduce harm to the environment. With the planned desulphuration process, the resultant tailings will provide ideal cover materials for reclaiming Doyon tailings areas. The benefits include reducing the cost of decommissioning the Doyon tailings facilities, providing a proven closure option for the Doyon mine and minimizing the biodiversity impact by not having to construct a new tailings facility.
Ore processing will be carried out at the existing Doyon carbon-in-pulp (CIP) mill complex, but the project will be split into two phases.In the first phase, only the gold mineralization will be treated at the mill. The Mouska copper circuit will be temporarily converted to a desulphuration circuit and cyanide destruction capacity will be increased to treat the generated tailings. In the second phase, the capacity of the existing copper flotation circuit will be increased, a zinc flotation circuit will be added and a new desulphuration circuit will be set up to begin tailings reclamation. All the cyanide will have to be destroyed because it is not compatible with the desulphuration and paste backfill processes.
Desulphuration is a process that involves non-selective flotation of all sulfides present in the tailings. The result of the desulphuration process is a sulfide concentrate that will go to the paste backfill plant and a final tailing exempt from sulfides that will be pumped to the tailings ponds. The existing paste backfill plant from Doyon will be relocated nearer to the Westwood shaft.
The ore will be sent by truck to the Doyon mill to be crushed and ground. The ore grinding circuit will utilize the existing SAG mill and a 1,000 HP ball mill.The Doyon mill produced up to 250,000 ounces of gold per year in the 1990s, so the existing gold recovery circuit will have more than enough capacity to recover the annual gold production from Westwood.
DOWNLOAD
IAMGold-NA-June11-Bro-s.pdf